ASME B31.3/PCC-2 API 570 Fabrication, Repair, & Regulations
Requirements for New Fabrication, Maintenance Repair, and Regulations
or
In-Person Attendance at:
Holiday Inn Express Calgary NW - University Area
2373 Banff Trail NW
Calgary AB T2M 4L2 Canada
587-390-6100
Attendance Options
Remote Online Attendance:
participants attend remotely (from home or workplace) and interact with the live instructor through an online video meeting on the scheduled instructor-led training dates.
In-Person Attendance:
participants attend in-person (at the Holiday Inn Express Calgary NW - University Area location) and interact with the live instructor on the scheduled instructor-led training dates.
IMPORTANT:
Please be aware that there are two different CASTI courses available on the subject of ASME B31.3 Process Piping. Review the course description below and compare it to our ASME B31.3 Code Design Requirements course before registering.
Learning Outcomes [+]
Participants who successfully complete this course will be able to:
- navigate and identify the CSA B51, Alberta Safety Code Act, Pressure Equipment Safety Regulations (PESR), and other jurisdiction rules related to ASME codes and standards for new construction, in-service repair, and alteration of pressure piping;
- navigate, identify, and apply ASME B31.3 new construction fabrication welding rules of:
- Chapter III Materials,
- Chapter V Welding Fabrication,
- Chapter VI Inspection and Examination, and
- Chapter VI Leak Testing.
- navigate, identify, and apply API 570 and ASME PCC-2 welding repair rules of:
- API 570 Piping Welding Repair, and
- ASME PCC-2 Piping Welding Repair.
- review welding rule comparisons between ASME B31.3, PCC-2, and API 570.
This course will assist manufacturers in meeting the personnel competency and training requirements of AB-518, Rev. 1, Pressure Piping Construction Requirements.
Who Should Attend
Engineers, inspectors, maintenance and QA personnel, NDE technicians, experienced tradespeople, who work for owner-user companies, EPCs, inspection companies, fabricators, maintenance service and repair companies, and inspection companies from refineries, upgrader plants, oil sands plants, SAGD plants, petrochemical plants, power plants, gas/oil pipeline companies, pulp mills, repair and maintenance shops, equipment manufacturers, third party inspection and NDE companies, and all supporting industries. This course will also assist CSA W178.2 exam candidates who plan to write the code exam.
Continuing Professional Development (CPD) Hours
Participants will receive a digital CASTI Certificate of Completion, awarding 24 CPD hours, for attending all 3 days of the scheduled training. Note: CPD (Continuing Professional Development) hours are equivalent to PDH (Professional Development Hours).
Course Outline [+]
Introduction to Laws, Regulations, Jurisdiction and Related Codes and Standards
- hierarchy of related regulations, codes, and standards
- brief introduction to CSA B51, Part 1, Alberta Safety Code Act, Alberta Pressure Equipment Safety Regulations (AB-516 PESR User Guide)
- ABSA's role as the Alberta Jurisdiction Administrator and Authorized Inspection Agency
B31.3 Responsibilities
- owner, designer, manufacturer, fabricator, erector, and owner's inspector
B31.3 Materials and Requirements
- B31.3 listed, unknown, and reclaimed materials terms and definitions
- ASTM A106 (A530) and A333 (A999) carbon steel piping
- ASTM A105 and A350 (A961) carbon steel forged fittings and flanges
- Material Test Reports (MTRs)
- review of sample A105, A106, and A333 MTRs
ASTM and ASME Multiple Marking Rules
- ASME Section II, Part A, Mandatory Appendix III Guidelines on Multiple Marking of Materials
- ASTM multiple marking rules in A182 (A961)
Workshop
- ASTM specifications
Introduction to B31.3 Impact Testing Requirements
- design minimum and maximum temperature
- Table 323.2.2 Requirements for Low Temperature Toughness Tests for Metals
- Figure 323.2.2A Minimum Temperatures Without Impact Testing for Carbon Steel Materials
- Table 323.3.1 Impact Testing Requirements for Metals
- ASTM A370 Charpy impact testing procedure for steel products
Workshops
- determine impact testing exemption temperature
- determine impact testing acceptance criteria
Welding Metallurgy
- defining the weldment zones: WMZ (mixed and unmixed), Weld Interface, HAZ, BMZ
- weldability, use of carbon equivalent and ferrite number
- heat input of welding and influence on mechanical properties and corrosion resistance
- welding residual stress and joint design
B31.3 Fabrication Welding
- responsibilities
- brief review of ASME Section IX WPS qualifications for carbon steels
- AWS Filler Metal Specifications
- cleaning, end preparation, alignment, trimming, root spacing, tack welds, peening
- branch connection welds and sizing
- flange attachment welds
- weld repair during fabrication
- installation of set-through and set-on nozzles, including weldolet or threadolet
- preheat requirements
- postweld heat treatment requirements
API 570-ASME PCC-2 Piping Welding Repair
- PCC-2, Article 304: Flaw Excavation and Weld Repair
- API 570, 8.2.3.2 Preheating
- API 570, 8.2.4 Preheating Alternatives in Lieu of PWHT
- API 570, 8.2.3.3 Postweld Heat Treatment
- API 570, 8.2.4 Control Deposition Welding Alternatives in Lieu of PWHT
- PCC-2, Article 209 Alternatives to Postweld Heat Treatment
- API 570 Repair, Major Repair, Permanent and Temporary Repairs, Alteration definitions
- PCC-2, Article 206 Full Encirclement Steel Reinforcing Sleeves for Piping
- API 570, 8.1.4.1 and Figure C.1 encirclement-welded split-sleeve repair
- PCC-2, Article 210 In-Service Welding Onto Carbon Steel Pressure Components or Pipelines
- PCC-2, Article 211 Weld Buildup, Weld Overlay, and Clad Restoration
B31.3 Inspection and Testing for New Construction
- responsibilities of the fabricator, purchaser, and inspector
- introduction to examination extent and methods
- Table 341.3.2 Acceptance Criteria for Welds
Workshop
- practice using Table 341.3.2
B31.3 Leak Testing for New Construction
- general requirements
- preparation for leak testing
- brittle fracture considerations for leak testing
- hydrostatic testing
- closure welds, 345.2.3(c) and AB-519
- pneumatic testing
- AB-522 Standard Pneumatic Test Procedure Requirements for Piping Systems
- PCC-2, Article 501 Pressure and Tightness of Piping and Equipment
- PCC-2, Article 502 Nondestructive Examination in Lieu of Pressure Testing for Repairs and Alterations
Learning Assessment
Learning self-assessment is performed through discussions, problem solving exercises, and workshops.
Required Code Documents
All participants must bring the ASME B31.3 code to this class. If you require a copy, it can be purchased from CASTI when you register for the course.
Course Notebook
A digital course notebook will be provided to all participants by CASTI (printed hardcopy not available).
About the Instructor
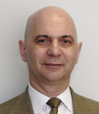
John E. Bringas, P.Eng. is the President and Founder of Codes and Standards Training Institute (CASTI) and CASTI Publishing Inc. He is a professional engineer who has practiced metallurgical and materials engineering, and inspection since 1975. He has also been certified as an API 510, 570, 653, 571, 577, and 580 inspector, an AWS Certified Welding Inspector, an Alberta In-Service Pressure Vessel Inspector and Welding Examiner, and CGSB certified NDE examiner in UT and RT. He is a long-time committee member of ASTM A01 Steels, A05 Coated Steels, B02 Nonferrous Alloys, E04 Metallography, E28 Mechanical Testing, F42 Additive Manufacturing, J01 ASTM/NACE Committee on Corrosion, NACE STG 31 Oil and Gas Production—Corrosion and Scale Inhibition, STG 32 Oil and Gas Production-Metallurgy, STG 34 Petroleum Refining and Gas Processing, STG 35 Pipelines, Tanks, and Well Casings, STG 39 Process Industries—Materials Applications and Experiences, and past Canadian Representative on ISO TC 17-SC 4 (Steels). He is the author of the ASTM Handbook of Comparative World Steel Standards, ASTM Handbook of Steel Data: American and European, ASTM Passport to Steel Database, and the CASTI Metals Data Books. Mr. Bringas has engineering work experience in the steel making, foundry, consulting (failure analysis), inspection, NDE, refinery, pipeline, and petrochemical industries.